The history of printing is rich and fascinating, dating back to ancient civilizations. From the Sumerians and Egyptians imprinting images on clay tablets to the invention of the printing press, these historical techniques have shaped the way we communicate and share information.
Let's take a journey through the past and explore the old style of printing, understanding how it has evolved over time.
Key Takeaways:
- Woodblock printing is one of the earliest forms of printing, originating in China around 200AD.
- Movable type revolutionized printing by allowing individual letters to be configured and placed together.
- Johannes Gutenberg's invention of the printing press in the 15th century revolutionized the industry and led to mass book production.
- The Gutenberg Bible marked a significant milestone as the first mass-produced book.
- Various printing techniques, such as etching, lithography, and screen printing, have contributed to the advancements in the field.
Woodblock Printing – 200AD
Woodblock printing is one of the earliest forms of printing, dating back to around 200AD in China. This vintage printing technique involves carving a design into a block of wood and inking the raised parts. The ink is then transferred onto paper or fabric by applying pressure, creating beautiful and intricate designs.
This printing method played a significant role in the spread of knowledge and book production. As it gained popularity, woodblock printing techniques were adopted in Europe, contributing to the development of the printing industry.
“Woodblock printing laid the foundation for later printing techniques and played a crucial role in the dissemination of information throughout history.”
How Woodblock Printing Works:
Woodblock printing involves several steps:
- Carving: A design is meticulously carved into a block of wood.
- Inking: The raised parts of the block are inked using a brush or a roller.
- Printing: The inked block is pressed onto paper or fabric, transferring the design.
Woodblock printing allowed for the mass production of books, making printed materials more accessible and facilitating the exchange of ideas and knowledge.
Advantages of Woodblock Printing | Disadvantages of Woodblock Printing |
---|---|
|
|
Woodblock printing laid the foundation for more advanced printing techniques and continues to be appreciated for its artistic qualities.
Movable Type – 1041
In the world of printing, innovation has always been a catalyst for change. One such groundbreaking invention was movable type, which revolutionized the way information was disseminated. The credit for this ingenious technique goes to Bi Sheng, a Chinese inventor who introduced movable type during the Song dynasty in 1041.
Movable type allowed individual letters to be configured and placed together in any order, providing a flexible and efficient way of printing. This breakthrough eliminated the need for handwritten script, making the printing process faster and more accurate. Initially, movable type was crafted from clay, allowing for simple yet effective printing. However, as the demand for clearer and more durable printing grew, the transition to wood and metal types became inevitable, paving the way for enhanced printing quality and legibility.
“Movable type transformed the world of printing, marking a shift from labor-intensive handwriting to a more efficient and standardized process.”
The emergence of movable type had a profound impact on script printing, streamlining the production of books, pamphlets, and other printed materials. With the ability to easily rearrange individual letters, printers could create multiple copies of a document without having to rewrite the entire content repeatedly.
Benefits of Movable Type
- Diverse Typography: Movable type allowed for various font styles and sizes, enriching the visual appeal of printed materials.
- Reusability: Unlike earlier methods, movable type could be reused multiple times, enabling cost-effective and efficient printing.
- Standardization: The uniformity of letterforms facilitated consistency in printed texts, improving readability and comprehension.
Bi Sheng's invention of movable type marked a significant milestone in the history of printing, paving the way for further advancements in the field. This innovative technique laid the foundation for the development of more sophisticated printing methods, eventually leading to the invention of the printing press by Johannes Gutenberg.
Advantages of Movable Type | Disadvantages of Movable Type |
---|---|
1. Diverse typography options | 1. Time-consuming typesetting process |
2. Reusability of individual letters | 2. Fragility of wooden and clay types |
3. Standardization of printed texts | 3. Limited character sets and languages |
The First Ever Printing Press – 1440
In 1440, Johann Gutenberg introduced the world to the first printing press, revolutionizing the way information was disseminated. Combining movable type, previously used in China, with mechanical presses, Gutenberg's invention enabled faster and more efficient printing.
With the printing press, Gutenberg made it possible to produce books at an unprecedented rate. This breakthrough in mass production transformed the accessibility of printed materials and had a significant impact on spreading knowledge and promoting literacy.
Johann Gutenberg's printing press marked a turning point in the history of communication and laid the foundation for the development of the modern printing industry. Through his ingenuity and innovation, Gutenberg paved the way for the printing revolution that would shape the world in the centuries to come.
“The printing press is the ultimate gift of man, giving us the ability to document our thoughts, share ideas, and preserve knowledge for future generations.” – Johann Gutenberg
Iconic Print Moment – ‘The Gutenberg Bible' – 1455
The Gutenberg Bible, printed in 1455, is a monumental achievement in the history of printing. This masterpiece represents the first mass-produced book, marking a significant milestone in the development of the printing press and movable type.
The Gutenberg Bible, also known as the “42-line Bible” due to the number of lines per page, was printed by Johann Gutenberg in Mainz, Germany. It was the result of several years of meticulous craftsmanship and innovative techniques.
“The printing press is the greatest weapon in the armory of the modern commander.” – T.E. Lawrence
Using moveable type, Gutenberg meticulously crafted each individual letter, punctuation mark, and symbol which allowed for the efficient reproduction of the text. The Gutenberg Bible was a remarkable example of unparalleled precision and attention to detail.
The Gutenberg Bible showcased the capabilities of the printing press by producing approximately 180 copies, a substantial number for that time. Its completion marked a turning point in history, demonstrating the power of the printing press to disseminate information on a large scale and make books more accessible.
The Historical Significance of the Gutenberg Bible
The Gutenberg Bible not only revolutionized the way books were produced but also had far-reaching implications for literacy, education, and the spread of ideas. Its impact on society cannot be overstated.
- Preservation of Knowledge: The mass production of Bibles and other written materials enabled the preservation and distribution of knowledge. Previously, books had to be painstakingly copied by hand, making them rare and expensive. The Gutenberg Bible allowed for wider access to sacred texts and fueled the advancement of various fields of study.
- Cultural and Religious Influence: The Gutenberg Bible played a vital role in shaping the religious and cultural landscape of Europe. The dissemination of religious texts enabled individuals to interpret and engage with religious teachings in their native languages. This, in turn, spurred the Protestant Reformation and influenced the development of vernacular literature.
- Printing and Publishing Industry: The success of the Gutenberg Bible laid the foundation for the printing and publishing industry. Gutenberg's invention sparked a wave of technological advancements, attracting craftsmen and entrepreneurs who further refined the printing press and introduced new techniques, shaping the future of the industry.
The Gutenberg Bible is a testament to the transformative power of printing. Its significance extends beyond its intrinsic value as a religious text; it symbolizes a fundamental shift in the way information is shared and consumed, a catalyst for the dissemination of knowledge and ideas that continues to impact society today.
Key Facts about the Gutenberg Bible | |
---|---|
Year of Printing | 1455 |
Printing Technique | Movable Type |
Number of Copies Produced | Approximately 180 |
Language | Latin |
Pages | 1282 |
Size | Folio |
Etching – 1515
Etching is a fascinating printmaking technique that has its roots in the Middle Ages. Initially used for decorating metal arms and armor, etching gained popularity as a method for printmaking in the early 16th century. One of the key figures in popularizing etching was German craftsman Daniel Hopfer.
To create an etching, an artist begins by coating a metal plate with an acid-resistant substance, usually wax. The artist then uses a sharp tool to draw the desired design on the plate, exposing the metal beneath the protective layer. Next, the plate is immersed in an acid bath, which etches the design into the exposed metal. Afterward, ink is applied to the plate, filling the etched grooves. The final step is to press the inked plate onto paper, transferring the design and creating the etching print.
Etching allows artists to achieve intricate details and delicate lines that may be challenging to achieve with other techniques. It provides a unique opportunity for artistic expression and experimentation. The process allows for multiple prints of the same design, making etchings a valuable addition to the world of printmaking.
Etching in Action
Etching combines the precision of drawing with the rich, textured finish of printmaking. It offers artists a unique way to bring their creative visions to life.
The Influence of Daniel Hopfer
Daniel Hopfer's contributions to the world of etching were significant. He not only refined the technique but also expanded its possibilities. Hopfer's work introduced innovative approaches to shading, cross-hatching, and tonal variations in etchings. His experimentation and technical expertise paved the way for future generations of printmakers.
Today, etching continues to be a popular printmaking technique, valued for its artistic versatility and expressive power. Artists across the globe explore the possibilities of etching, creating unique and captivating prints that resonate with audiences.
Lithography – 1790s
Lithography, a revolutionary printing technique developed in the late 18th century, introduced a new way to transfer ink onto paper using the principle of oil and water repulsion. This technique, discovered by Alois Senefelder, opened up endless possibilities for artistic expression and mass production of images.
To create a lithograph, an image is drawn on a stone or metal plate using an oil-based medium. The plate is then treated with a solution that repels ink except where the image is drawn. This ink-repellent solution is usually a mixture of gum arabic and acid. When ink is applied to the plate, it adheres only to the drawn areas, while the remaining areas repel the ink.
After the ink is applied to the plate, a piece of paper is placed on top, and pressure is applied, transferring the ink from the plate onto the paper. However, direct contact between the plate and the paper can cause damage, so a rubber blanket is often used as an intermediary. The ink is first transferred from the plate to the rubber blanket and then onto the paper, ensuring a clean and precise image transfer.
Lithography, with its ability to produce high-quality prints with fine details and a range of tonal values, quickly gained popularity among artists and printmakers. The technique allowed for the reproduction of artworks on a larger scale, making art more accessible to a wider audience.
Lithography | Advantages | Disadvantages |
---|---|---|
Allows for precise and detailed image reproduction | Vegetable-based inks provide a wide range of vibrant colors | Requires skilled artisans to prepare and print the plates |
Enables mass production of images | Can be used on various materials like paper, fabric, and metal | Can be time-consuming due to the intricate process involved |
Offers the ability to create unique textures and gradients | Allows for easy correction and alteration of the image | Requires specialized equipment and materials |
The development of lithography had a profound impact on the art world and commercial printing. It allowed for the production of intricate illustrations, colorful posters, and detailed maps. One notable figure in the history of lithography is Godefroy Engelmann, a French inventor who made significant contributions to the technique's refinement and popularization.
The Rotary Press – 1843
In 1843, Richard March Hoe invented the revolutionary rotary press, a game-changing technology that transformed the printing industry. This innovative machine, with its unique cylindrical plates, allowed for continuous paper feeding, significantly increasing printing speed and efficiency.
The rotary press replaced the slower hand-operated printing presses, ushering in a new era of rapid and continuous production of printed materials. By using curved plates that seamlessly accommodated the continuous feed of paper, the rotary press eliminated the need for stopping the machine after every impression, resulting in a much faster and more streamlined printing process.
The continuous paper feeding feature of the rotary press enabled printers to produce large volumes of printed materials in a shorter period, making it easier and more cost-effective to meet the growing demand for books, newspapers, and other printed materials.
“The rotary press was a game-changer in the printing industry. Its continuous paper feeding capability allowed for faster and more efficient production of printed materials, revolutionizing the way printing was done.”
Richard March Hoe's invention of the rotary press marked a significant milestone in the history of printing. It propelled the industry further, paving the way for even more advanced technologies and processes that would follow.
Advantages of the Rotary Press | Disadvantages of the Rotary Press |
---|---|
Significantly improved printing speed | Initial cost of the machinery |
Continuous paper feeding for uninterrupted production | Requires skilled operators for maintenance |
Efficient production of large volumes of printed materials | Occupies more space compared to smaller presses |
Impact of the Rotary Press
The rotary press revolutionized the printing industry, enabling faster, more efficient, and cost-effective production of books, newspapers, magazines, and other printed materials. It played a significant role in meeting the increasing demand for printed materials during the industrial revolution.
Furthermore, the rotary press facilitated the widespread dissemination of information, contributing to the spread of literacy and knowledge among the masses. It revolutionized the publishing industry by making books more accessible and affordable, fostering education, and enabling the cultural exchange of ideas on a global scale.
The continuous paper feeding technology developed by Richard March Hoe paved the way for future advancements in printing technology, laying the foundation for the modern printing systems that we use today.
Offset Printing – 1875
Offset printing, developed in 1875, revolutionized the printing industry by introducing the concept of offset ink transfer. In this technique, the ink is transferred from a plate to a rubber blanket before being applied to the printing surface. Offset printing is commonly used for large print runs and provides high-quality, sharp images.
Advantages of Offset Printing:
- High-quality image reproduction
- Consistent color accuracy
- Ability to use a wide range of substrates
- Cost-effective for large print runs
- Faster printing speed
Offset printing utilizes the principle of lithography, where the ink is offset from the plate onto a rubber blanket and then onto the printing surface. This process allows for precise ink transfer and results in sharp, vibrant images.
Offset printing is a versatile printing method that is suitable for various applications, including magazines, brochures, catalogs, and packaging materials.
The use of a rubber blanket in offset printing provides several advantages. The rubber blanket helps to ensure consistent ink transfer, reduces the risk of ink smudging, and allows for printing on uneven surfaces. The offset printing process also allows for quick drying of the ink, resulting in faster production times.
Offset Printing Process:
- Prepress: The design is created using computer software and prepared for printing.
- Plate Making: Metal plates are made from the design, with each plate representing a color in the final print.
- Ink Preparation: Ink is mixed to match the desired colors for the print job.
- Printing Press Setup: The plates are installed onto the printing press, and the rubber blankets are adjusted for proper ink transfer.
- Ink Transfer: Ink is transferred from the plates to the rubber blankets and then onto the printing surface.
- Drying and Finishing: The printed materials are dried and may undergo additional finishing processes, such as trimming or binding.
Offset printing has remained a popular choice for high-volume print jobs due to its efficiency, cost-effectiveness, and ability to deliver consistent, high-quality results.
Screen Printing – 1910
Screen printing, also known as silk screening, has ancient origins in China but gained popularity in Europe in the early 20th century when silk stock became more widely available. This technique involves pushing ink through a mesh stencil onto textiles or paper. Screen printing is commonly used for t-shirt printing and other types of fabric printing.
Advantages of Screen Printing
- High-quality prints: Screen printing allows for vibrant colors and sharp details, making it ideal for creating intricate designs on fabric.
- Durability: The ink used in screen printing is highly durable and can withstand regular washing and wear, making it a popular choice for clothing items.
- Versatility: Screen printing can be used on a wide range of materials, including cotton, polyester, and even metal surfaces, opening up endless possibilities for customization.
The Screen Printing Process
The process of screen printing involves several steps:
- Preparing the screen: A fine mesh screen, commonly made of silk or synthetic fibers, is stretched tightly onto a frame.
- Creating the stencil: A stencil is created on the screen using a light-sensitive emulsion or by cutting out the design from an adhesive vinyl sheet.
- Ink preparation: The desired colors are mixed to achieve the desired shades and consistency.
- Printing: The ink is placed on top of the screen, and a squeegee is used to push the ink through the stencil onto the fabric or paper.
- Drying and curing: The printed material is left to dry, and heat may be applied to cure the ink, ensuring its longevity and durability.
Screen printing offers excellent color saturation, a wide range of color options, and the ability to print on various types of surfaces. It is a versatile and reliable printing technique that continues to be widely used in the textile industry.
Inkjet Printing – 1951
Inkjet printing, developed in 1951, revolutionized the printing industry with its innovative approach. Unlike traditional printing methods that required direct contact with the printing surface, inkjet printers introduced a new way of applying ink. Using spray jet technology, these printers precisely spray ink through small jets onto the printing surface, resulting in high-quality and precise prints.
Inkjet printing has gained widespread popularity in both home and office settings due to its versatility and efficiency. It is particularly favored for color printing, as it allows for vibrant and richly detailed images. With inkjet printers, individuals and businesses can easily produce professional-quality prints without the need for complex and time-consuming setups.
One of the key advantages of inkjet printing is its non-contact printing method. With no direct contact between the printing mechanism and the surface, there is less risk of damage or smudging, ensuring clean and flawless prints. This makes inkjet printing ideal for printing on various materials, including paper, fabric, and even plastics.
“The beauty of inkjet printing lies in its ability to create prints with exceptional detail and color accuracy, making it an invaluable tool for artists, photographers, and designers.”
Inkjet printers operate by propelling tiny droplets of ink onto the printing surface. These droplets are precisely controlled and combined to create the desired image or text. The technology behind inkjet printing has evolved over the years, with advancements in print head design, ink formulations, and print speed, resulting in improved print quality and efficiency.
Today, inkjet printing is not only limited to paper-based prints but also extends to various applications such as textile printing, signage, packaging, and even 3D printing. The versatility and accessibility of inkjet technology have made it an indispensable tool in many industries.
The Advantages of Inkjet Printing:
- High-quality prints with vibrant colors and sharp details
- Non-contact printing method, minimizing the risk of damage or smudging
- Wide range of printable materials, including paper, fabric, and plastics
- Quick and easy setup, suitable for both home and office use
- Versatile applications beyond traditional paper printing
Example of Inkjet Printer:
Brand | Model | Key features |
---|---|---|
Epson | EcoTank ET-4760 |
|
Canon | PIXMA TS9120 |
|
HP | OfficeJet Pro 9025 |
|
With the constant advancements in inkjet printing technology, we can expect even more impressive developments in the future. From improving print speed and quality to expanding the range of printable materials, inkjet printing continues to play a vital role in meeting the diverse printing needs of individuals and businesses.
Conclusion
Throughout history, the evolution of printing techniques has shaped the way we communicate, share information, and access knowledge. From the humble beginnings of woodblock printing and movable type to the modern marvels of digital printing, the printing industry has played a pivotal role in the dissemination of information and the spread of culture.
Printing has enabled the mass production of books, making literature and educational resources more accessible to people around the world. It has allowed for the preservation of historical records and the sharing of ideas, driving innovation and progress in countless fields.
As technology continues to advance, the future of printing holds even more exciting possibilities. From 3D printing that brings concepts to life in tangible forms to advancements in digital printing that deliver high-quality images with precision, the printing industry is poised to make further strides in the years to come.
In conclusion, the rich history of printing is a testament to the power of human ingenuity and the desire to share information. From ancient civilizations to modern times, printing has served as a catalyst for progress and a medium through which ideas are brought to life. As we look ahead, we can only imagine the remarkable innovations and advancements that lie on the horizon for the world of printing.
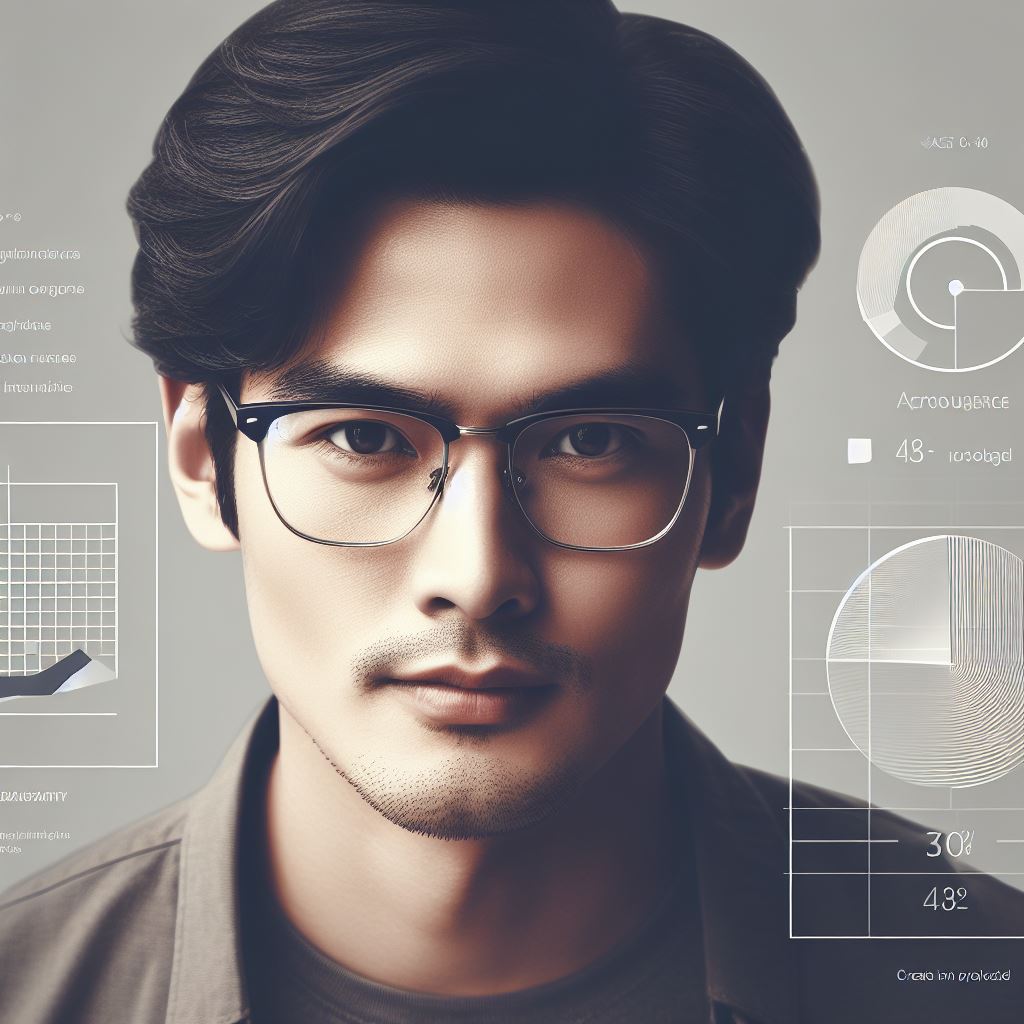
Morgan Azhari, the owner of PrinterUpdate.net, is a dedicated expert in the field of printers, leveraging a wealth of experience and education to create a platform that passionately shares insights and solutions.
With a goal to enhance the printer user experience, my vision for the website is to provide valuable content, making a positive impact on individuals navigating the complexities of printers.